Obținerea metalelor- metalurgia
Obținerea metalelor- metalurgia
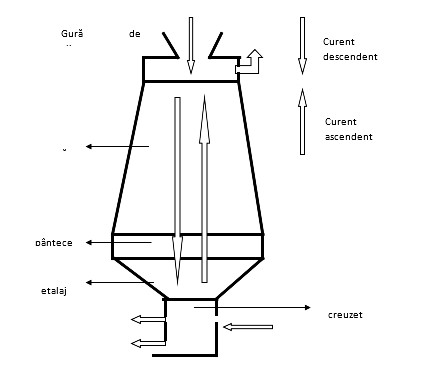
. Schema de principiu a unui furnal (Zapan, 1977).
Obținerea fontei
Procedeul se bazează pe reducerea oxizilor de fier cu cărbune în furnale înalte de dimensiuni mari, căptuşite cu cărămizi refractare. Furnalul constituie agregatul propriu-zis destinat producerii fontei necesare procesului de elaborare a oţelului în convertizor. Furnalul are forma a două trunchiuri de con, unite la baza lor având înălţimea de 20-30 cm. El este construit din cărămidă refractară, argilo-silicioasă, şi îmbrăcat într-o manta metalică sub formă de inele. Trunchiul superior se numeşte cuvă, iar cel inferior etalaj. În partea de jos a etalajului se află creuzetul, în care se adună fonta şi zgura topită (Zapan, 1977). Un furnal înalt funcţionează neîntrerupt câţiva ani în regim continuu (alimentare şi luare de probe, totuşi discontinue şarje), principiul de funcţionare fiind în contracurent:
- un curent descendent: materii prime şi materiale auxiliare şi fierul topit;
- un curent ascendent: gazele de furnal şi aerul cald.
- Produsul final este fonta care poate fi:fontă de turnătorie sau fonte cenuşii
- fonte de afinare sau fonte albe
- feroaliajele
Produse secundare sunt gazele de furnal: N2, CO, CO2 , SO2, H2, CH4 şi zgura.
Zgura se formează din: sterilul minereului, cenuşa cocsului, fondant, sulfură de mangan şi sulfura de calciu, acumulate în urma procesului de desulfurare (Zapan, 1977). Compoziţia zgurii depinde de calitatea fontei, compoziția încărcăturii, tipul sterilului şi tipul combustibilului. Ea poate fi acidă (obţinută la furnalele cu mangal) sau bazică (obţinută la furnalele cu cocs).
Figura 7. Flux tehnologic obţinerea fontei şi a oţelului
minereu de fier, fondant, cocs, aer
Fe3O4, Fe2O3, FeCO3, FeS2
reducere (în furnal)
FONTA
zgură
gaze de furnal
încălzirea aerului
Fonta albă
(75-80%)
Fonta cenuşie
(15-20%)
OŢEL
Gazul de furnal este al doilea produs secundar al furnalului cu următoarea compoziţie: 8-15% CO2, 24-30% CO, 3-5% H2, 0,2-0,4 CH4, 50-60% N, 10-50 g/m3N praf, 20-30 g/m3N vapori de apă.
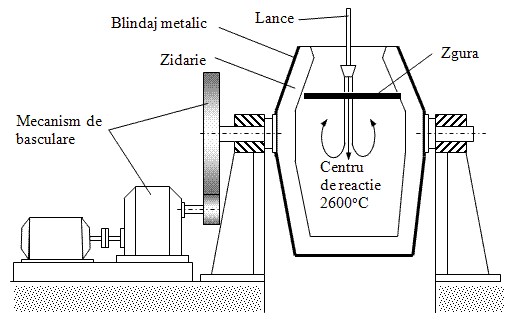
Schema
convertizorului cu oxigen LD (Gurău)
Obținerea oțelului
Procesul se bazează pe oxidarea carbonului şi a elementelor însoţitoare din fonta lichidă cu ajutorul oxigenului. Primele convertizoare, cele clasice au fost puse în funcţiune în 1854 – 1856 sub denumirea de convertizoare Bessemer şi Thomas, deosebirea dintre cele două constând în natura căptuşelii refractare (primul are căptuşeală acidă, iar cel de al doilea are căptuşeală bazică). Astăzi, se utilizează convertizorul cu oxigen, numit convertizor LD după uzinele din Linz Donovitz, în care a fost pus în funcţiune în anul 1952. În cazul acestor convertizoare insuflarea cu oxigen tehnic se face pe la partea superioară, printr-o lance de cupru cu pereţi dubli, protejată cu o teacă refractară şi puternic răcită cu apă. Se măreşte viteza de afinare, durata procesului fiind de 10-20 minute pentru o cantitate de fontă mult mai mare, se măreşte capacitatea agregatelor şi se evită infestarea cu azot şi alte elemente din aer a oţelului. În plus, acesta permite utilizarea deşeurilor metalice solide în încărcătură.
Tipuri de oţeluri:
- oţeluri carbon (OLC) - aliaje ale fierului cu carbonul cu un procent mai mic de 1,7%C iar impurităţile de Mn, Si, P şi S nu depăşesc 1%.
- oţeluri speciale (aliate) - aliaje ale fierului cu carbonul şi alte metale, sau un conţinut mare de Si şi Mn.
OL - Mn în procent mai mic de 14% - rezistenţă la uzură;
OL - Cr în procent mai mic de 13% - duritate, stabilitate la ruginire;
OL - Ni în procent între25-36% - rezistori electrici;
în procent 22% - rezistent la coroziunea apei de mare;
în procent 39% - confecţionarea instrumentelor de precizie;
OL - Cr aprox.18% - duritate, rezistenţă, stabilitate chimică;
OL - Ni aprox.8% - duritate, rezistenţă, stabilitate chimică;
OL - W între15-18% - fabricarea magneţilor permanenţi;
- stabilitate termică, rezistenţă;
- 5-7% - rezistenţă la fisurare;
OL – V în procent mai mic de 5% - stabilitate termică, rezistenţă;
- elasticitate, rezistenţă la rupere;
OL – Mo în procent între 0,25-9% - stabilitate chimică şi mecanică;
OL - Si în procent între1-4% - electrotehnică;
În procent între 4-5 %.- oţel tenace;
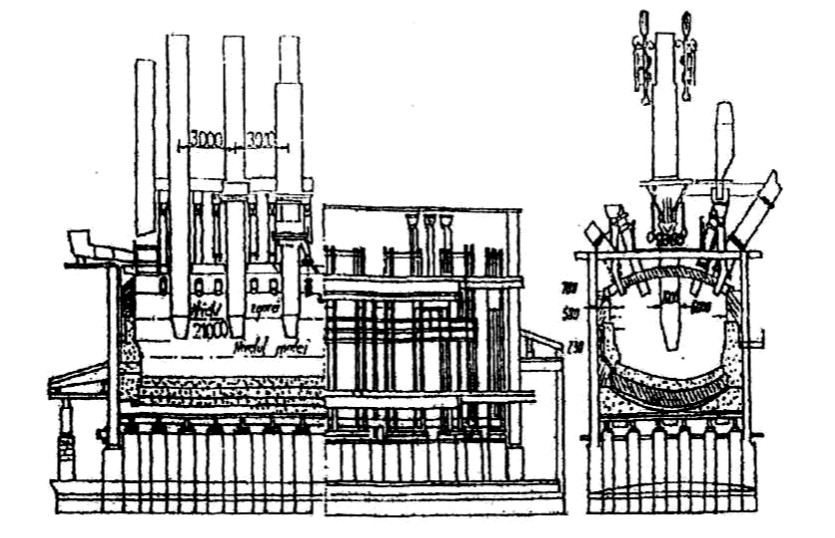
Cuptor electric cu arc pentru topirea cuprului
Obținerea cuprului
Cuprul se obţine din minereurile sulfuroase, în care mineralul principal este calcopirita, din minereurile oxidice, în care mineralele preponderente sunt malachitul şi azuritul şi din procesarea deşeurilor metalice (conductori , bobinaje din motoare). Având un conţinut scăzut de cupru (1–2% Cu), minereurile se concentrează prin flotaţie până la 15- 25% Cu), după care se prelucrează prin procedee hidrometalurgice sau pirometalurgice (Hătărăscu,1980). Cuprul brut obţinut se rafinează electrolitic,în vederea obţinerii cuprului de mare puritate.
Procedee pirometalurgice – se aplică minereurilor bogate în cupru. Acesta este obţinut prin reducerea cu cărbune a oxizilor de cupru în prezenţa sulfurii feroase şi a nisipului, prin procedeul matelor cuproase (Stoian, 2009).
Mata reprezintă o soluţie complexă de sulfuri în care componenţii principali suntCu2S şi FeS. Procedeul include următoarele operaţii principale: prăjirea parţială a concentratelor (a), topirea pentru mată (b), convertizarea matelor (c), rafinarea termică (d) şi rafinarea electrolitică (e).
Procedee hidrometalurgice – se folosesc în cazul minereurilor sărace în cupru şi deşeurilor care conţin cupru. Minereul se concentrează prin flotaţie, apoi se prăjeşte la o temperatură de 500-600ºC pentru a transforma sulfurile în sulfaţi. Minereurile oxidice şi carbonaţii se tratează cu soluţie de H2SO4 sau cu leşii alcaline. Fazele tehnologice sunt: pregătirea materiilor prime, solubilizarea, purificarea soluţiilor sau concentrarea prin extracţie cu solvenţi organici şi extracţia cuprului din soluţii prin cementare, extracţie electrolitică sau reducerea din soluţie.